Opinion | Why the semiconductor shortage hitting cars and smartphones won’t be the last
- The last big supply chain shock was 10 years ago when the Fukushima earthquake damaged operations at Renesas Electronics, the No 3 supplier of auto chips
- Besides higher manufacturing costs, the other factor working against second sourcing is consolidation in the chip industry
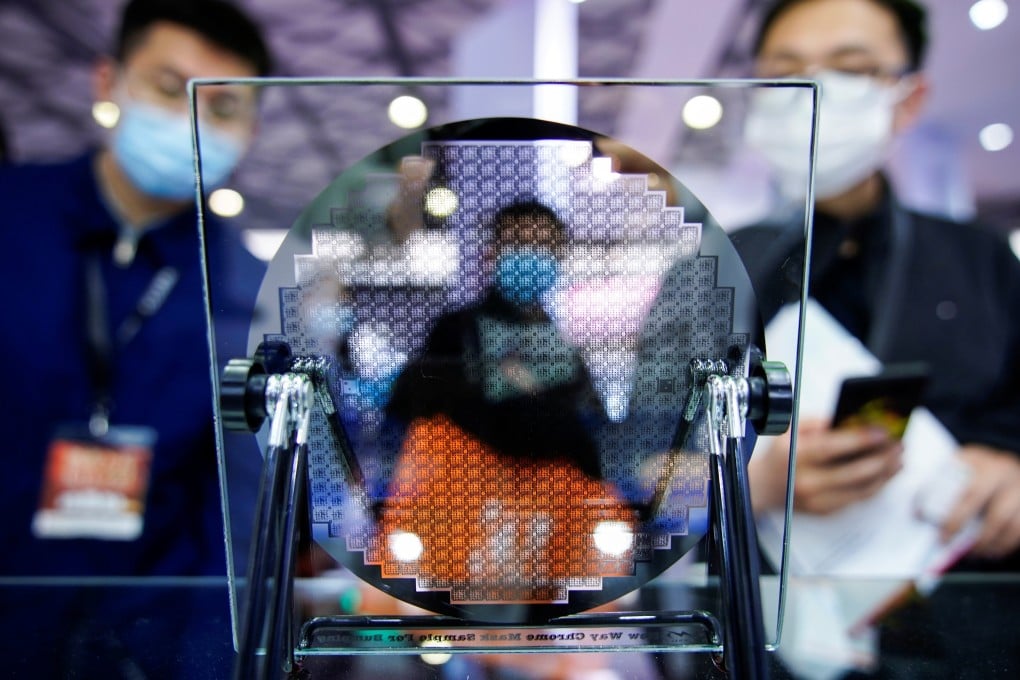
The supply chain shock came about after carmakers underestimated the rebound in demand amid the coronavirus pandemic. It was compounded by the fact that wafer foundries making the chips were fully booked and couldn’t ramp up production fast enough given the long lead times required to add wafer capacity.
The last time a similar supply chain shock hit the sector was 10 years ago when the Fukushima earthquake damaged wafer fab operations at Renesas Electronics, the No 3 supplier of automotive chips. That also triggered debate among chip suppliers about contingency plans for future disasters – specifically the need for second sourcing.
“This is not the first time people have thought about second sourcing. I’m not convinced that OEMs are ready to spend the money necessary. Second sourcing doesn’t come for free,” an executive at US auto chip maker Freescale Semiconductor was quoted as saying at the time.
Second sourcing simply means two different chip suppliers produce pin-for-pin compatible versions of the same device. If one source of supply is disabled for any reason, the second source can take up the slack and minimise supply chain disruptions.
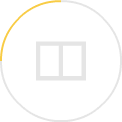