ALMINE stands out with hardest aluminium alloys
Japanese alloy manufacturer claims to produce the world’s hardest aluminium alloy wires and bars, and expects higher global demand for lighter, stronger parts for electric vehicles
[Country Business Reports interviews and articles by Discovery Reports www.discoveryreports.com]
Any company can fabricate aluminium alloys, but Japanese firm ALMINE stands out with its capacity to manufacture ultra-strong alloys to suit the special requirements of diverse industries, from high-rise construction to aerospace.
“We produce the hardest aluminium alloy wires and bars in the world,” says Takeshi Takeuchi, who replaced his father as president of ALMINE in 2014. “This distinct quality of our products sets us apart from our competitors.”
At the forefront of aluminium innovation, ALMINE has dedicated much time and research to maximise the metal’s potentials. ALMINE’s product development programme, which is one of the best in the world, has developed aluminium alloys such as its own duralumin concoction. Used in airframe fabrication and other safety-sensitive products, duralumin combines aluminium with copper, manganese and magnesium to produce an exceptionally hard aluminium alloy.
ALMINE also claims to be the only company in the world that manufactures two-tonne aluminium wires that have no joints from end to end. With diameters ranging from 9.5mm to 50mm, the seamless feature of the aluminium wire lends the product its superior strength.
ALMINE uses its continuous casting and rolling method, especially designed by Takeshi’s father, who is a machine engineer. Using an automatic tilting machine carefully calibrated for the whole production process, the continuous casting and rolling method ensures that only the precise amount of molten aluminium is poured into the production line. As such, ALMINE does not need to reheat the aluminium raw material, thus cutting the company’s CO2 emission by as much as only a third of the traditional process. The machinery also ensures that the aluminium molecules are dispersed evenly across the whole cross section of the wires. This feature prevents cracks and bends, a crucial safety requirement for aeroplane components.
“China is evolving and is starting to use better quality materials. With our rich experience in this regard, ALMINE is ready to support companies in China that require our products”
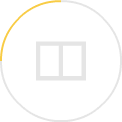