Companies rush to replace ‘just in time’ supply chains with ‘just in case’ contingencies as Covid-19 upends global manufacturing
- Industry players and supply chain experts said the shifting of the supply chain model is most likely in the production of essential goods such as food and medical devices
- Even as some firms look to disentangle their production networks from China, the country’s role in the global supply chain is too big to be replaced, say analysts
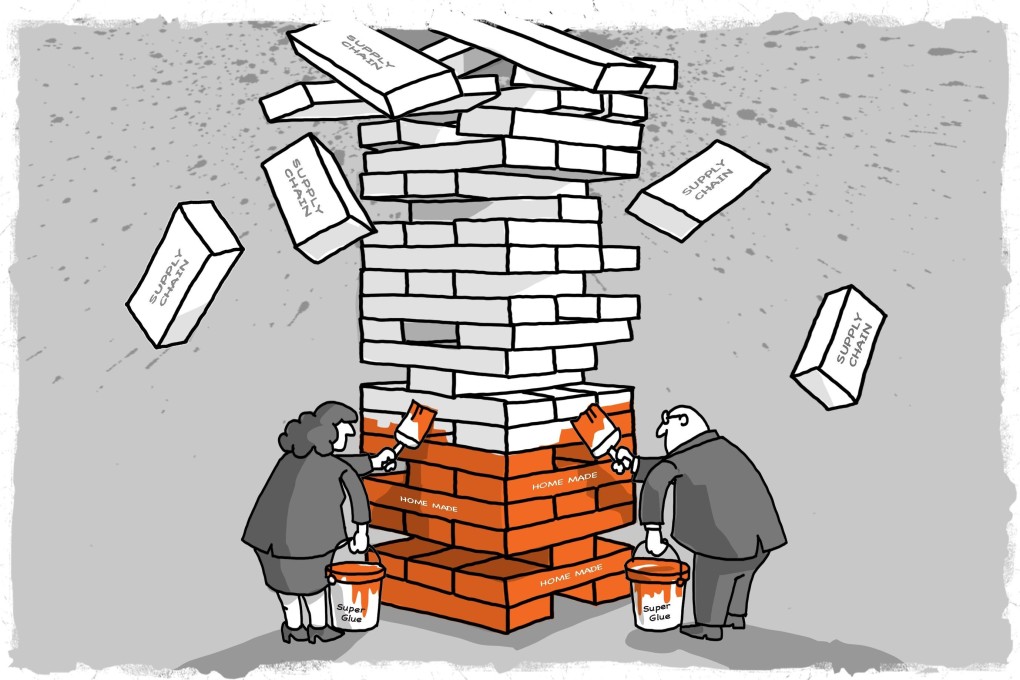
QYK Brands was putting the final touches on its US$5 million medical mask production line in Garden Grove, California, when it hit a snag: export shipments by its Chinese supplier of melt-blown polypropylene – the non-woven mesh that filters out airborne particles – were disrupted by extra inspections. China is its only source of supply, since all of the US fabric production combined can barely meet the needs of the largest face masks manufacturer in the country.
Supplies from Sinopec, China’s largest petrochemical producer and Chinese resellers of its products, trickled almost to a complete stop in early April, as Chinese customs inspectors scrutinised every overseas shipment of medical supplies and devices to ensure they meet export quality and protect China’s global reputation.
“There are plenty of suppliers in China, but only Sinopec is reliable [because] the rest are middle men buying and reselling it while marking the price up three to four times,” QYK’s chief executive Rakesh Tammabattula said in a telephone interview with South China Morning Post. “What’s more, there is no way we can authenticate the filtration effectiveness of the fabric because we cannot impose any requirement to test the products before they are delivered … we have to take the quality risk.”
Many companies had already moved or mulled the idea of shifting manufacturing facilities out of China after it became embroiled in a gruelling trade war with the US.
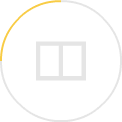